Material Positioning Systems are at the heart of automation and precision in today’s smart factories. As the manufacturing enterprise embraces Industry four.Zero, these structures are hastily evolving to aid extra connectivity, records evaluation, and manufacturing performance. The integration of AI, robotics, and IoT into fabric positioning approaches is helping factories lessen human mistakes, improve workflow, and allow real-time decision-making. With the increasing demand for velocity, safety, and precision, Material Positioning Systems are paving the way for smarter, more agile, and extra adaptive manufacturing environments which can be equipped to meet the destiny’s complicated industrial needs.
1. Rise of Smart Manufacturing and Role of Material Positioning Systems
Smart production has revolutionized how production strains perform, transitioning from conventional guide approaches to automatic, records-pushed systems. Material Positioning Systems are critical to this modification, enabling the correct and timely alignment of substances during production. These systems talk immediately with machines and software program platforms, lowering delays and ensuring that parts and merchandise flow seamlessly through each segment of production. As factories grow to be digitized, the mixing of intelligent positioning mechanisms becomes vital to keep competitiveness and agility within the international market.
2. Integration with IoT and Real-Time Data
The integration of the Internet of Things (IoT) has multiplied Material Positioning Systems to new stages of intelligence and connectivity. Through sensors, actuators, and networked gadgets, those systems can acquire and percentage statistics in actual time, optimizing selections and reducing downtime. Sensors screen role, vibration, temperature, and other factors to make sure unique manipulation over material glides. When mixed with cloud-primarily based analytics, this record allows predictive maintenance, reduces waste, and complements gadget performance. The result is a manufacturing facility ground which can quickly respond to shifts in demand or unexpected disruptions with minimum human intervention.
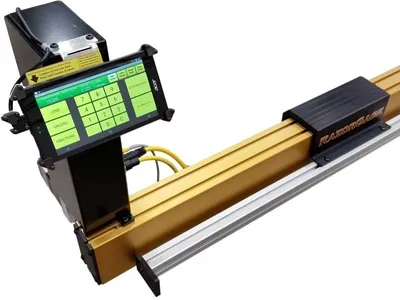
3. Enhanced Robotics Collaboration
The collaboration among Material Positioning Systems and robotic automation has created extra fluid and responsive manufacturing unit environments. Robots, whether or not self reliant cell units or robotic hands, rely on precise positioning inputs to have interaction with materials efficiently. These structures are manual robots in duties like picking, placing, welding, or assembling additives with high accuracy. In smart factories, this synergy results in steady output satisfactory and faster cycle times. As robotics become superior with machine learning talents, Material Positioning Systems will want to evolve in actual-time to assist dynamic robotic movements in complicated manufacturing settings.
4. AI-Driven Optimization for Positioning Accuracy
Artificial Intelligence is shaping the next generation of Material Positioning Systems by driving actual-time selection-making and continuous optimization. AI algorithms procedure considerable amounts of manufacturing facts to be expecting fabric flow, discover styles, and recommend upgrades. This allows systems to self-modify for accuracy and performance based totally on historic and live facts. In eventualities where production strains handle a couple of varieties of substances or rapidly trade configurations, AI permits adaptive positioning techniques that lessen setup time and decorate flexibility. This intelligence lets factories hold excessive throughput without compromising precision.
5. Energy Efficiency and Sustainability
Modern Material Positioning Systems are being designed with sustainability in mind. Smart positioning generation can notably reduce energy consumption by optimizing motion paths and minimizing unnecessary idle time. Advanced manipulate algorithms and servo structures permit smoother transitions and managed deceleration, saving each strength and mechanical put on. In a clever manufacturing facility in which sustainability is a priority, such systems contribute to environmental goals by way of reducing carbon footprints and aligning with green manufacturing requirements. The push for sustainable innovation ensures that destiny positioning systems will stabilise productivity with eco-aware layout.
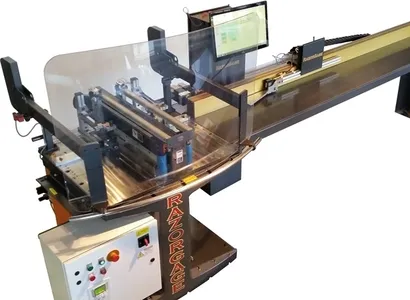
6. Adaptability to Custom and Small-Batch Production
As marketplace needs shift towards customization and smaller batch sizes, Material Positioning Systems must evolve to assist greater flexibility. Unlike conventional assembly lines designed for mass production, clever factories require structures that could quickly adapt to new designs and configurations. Positioning technology now leverage modular designs and programmable logic to reconfigure material paths with minimal downtime. This adaptability allows producers to produce custom designed products with the identical efficiency as standardized ones. The rise of modular and reconfigurable systems signifies a destiny in which customization no longer comes at the price of productivity.
7. Integration with Digital Twins and Simulation Models
Digital twins are virtual representations of physical systems that reflect real-global procedures in a virtual environment. Material Positioning Systems, when integrated with virtual twins, permit manufacturing facility operators to simulate modifications and test optimizations earlier than implementing them bodily. These simulations provide insight into how positioning systems will respond to new layouts, merchandise, or workflows. This predictive functionality reduces trial-and-error and ensures smoother transitions at some point of upgrades or shifts in manufacturing. By coupling simulation fashions with stay remarks from the bodily system, clever factories can constantly refine operations and expect destiny challenges.
8. Improved Worker Safety and Human-Machine Interaction
In contemporary factories, protection is as vital as speed and precision. Material Positioning Systems contribute to more secure work environments by means of decreasing the need for manual coping with and enhancing manage over transferring parts. With superior sensors and real-time monitoring, those structures can detect human presence and halt operations to save you injuries. Innovations in human-gadget interplay, including gesture recognition and wearable tech, further beautify safety and collaboration. Operators can now paint alongside machines with self belief, understanding that computerized systems are designed to respond intelligently to human inputs and environmental modifications.
9. Scalability and Interoperability in Multi-Plant Networks
For manufacturers operating a couple of centers or global supply chains, scalability and interoperability are important. Material Positioning Systems of the future may be designed to perform seamlessly across different production environments. Open verbal exchange protocols and standardized interfaces will permit these structures to percentage facts and characteristics across numerous platforms, machines, and locations. Cloud-based dashboards and centralized manipulate systems enable plant managers to display and modify positioning operations from any location. This interconnectedness guarantees regular exceptional and performance, irrespective of the physical vicinity of the manufacturing unit.
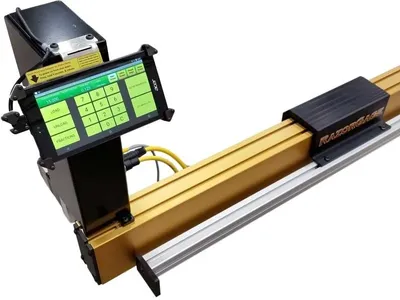
10. Innovations Leading to Greater Precision and Automation
The trajectory of Material Positioning Systems is moving towards greater precision, autonomy, and intelligence. Advanced technology such as laser-guided alignment, laptop imaginative and prescient, and adaptive servo management are getting mainstream. These innovations make sure that even the maximum complicated components are aligned with micron-stage accuracy. With automatic calibration and self-learning capabilities, future structures would require minimal human input even as keeping tremendous performance. This stage of automation additionally reduces the impact of operator variability and will increase the predictability of production outcomes.
In the end, the future of Material Positioning Systems in smart factories is promising and full of transformative capacity. As technologies evolve, these systems will become greater, wise, responsive, and vital to accomplishing operational excellence. Whether via AI, robotics, or digital twins, the improvements using positioning systems are aligning with the wider desires of Industry four.0. Notably, their function extends to enhancing protection systems including the automatic saw stop , where precision and speed are crucial to shielding both equipment and personnel. As those traits retain, smart factories could be defined by their potential to combine, adapt, and excel through the energy of subsequent-era Material Positioning Systems.