Heat exchanger components are crucial additives answerable for efficient thermal strength switch between fluids. Whether utilized in HVAC structures, chemical processing, or electricity era, the reliability of a warmness exchanger depends at the condition and compatibility of its internal elements. Spiral warmness exchangers, a sort of compact and highly green heat exchanger, rely on particular additives like spiraled metal plates, gaskets, and nozzles to preserve seamless warmness switch in tough business environments. Each part need to withstand severe temperatures, corrosive fluids, and strain fluctuations. Regular inspection and maintenance of those elements ensure lengthy-term performance and energy efficiency. Understanding each part’s characteristic helps operators pick out early signs and symptoms of damage and put in force well timed replacements. By that specialize in long lasting materials, accurate becoming, and professional installation, you could beautify the operational life of any warmth exchanger device.
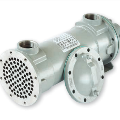
Importance of Plate and Shell in Heat Exchanger Systems
The plate and shell are of the most big heat exchanger parts, especially in plate-type and spiral heat exchangers. Plates serve as the medium thru which warmth trade occurs, at the same time as the shell affords structural aid and housing. In spiral heat exchangers, the spiraled plates shape channels that facilitate counterflow or crossflow between fluids, maximizing floor contact and minimizing space utilization. These components need to be corrosion-resistant and thermally conductive. Stainless steel and titanium are common fabric picks. Shells must manage internal pressure and external environmental situations with out deformation. Their layout additionally guarantees smooth get right of entry to for cleansing and inspection. When either the plate or shell suffers from degradation, it at once impacts the exchanger’s potential to transfer warmness correctly. Maintaining easy and intact plates and shells guarantees a smooth thermal trade and strength financial savings through the years.
Role of Gaskets in Heat Exchanger Performance
Gaskets play a vital role in sealing the joints between plates or sections of the heat exchanger, preventing fluid leaks and making sure safety. In spiral heat exchangers, gaskets are frequently used to separate glide paths and hold strain integrity within each channel. These heat exchanger components are normally made from rubber or polymer-primarily based materials which could resist excessive temperatures and chemical exposure. The effectiveness of gaskets relies upon on correct placement, material compatibility, and upkeep. A broken or improperly mounted gasket can result in operational inefficiencies or entire gadget failure. Over time, gaskets can emerge as brittle or compressed, necessitating timely inspection and alternative. Choosing fantastic gaskets appropriate for the operating surroundings extends the lifestyles of the warmth exchanger and maintains consistent overall performance. Their seemingly small position has a giant effect on the general effectiveness of the warmth switch machine.
The Function of Nozzles in Fluid Distribution
Nozzles are critical heat exchanger components accountable for guiding fluids into and out of the gadget. These entry and go out factors ensure proper distribution of beverages or gases across the heat exchanger surface. In spiral heat exchangers, the nozzle layout directly affects fluid dynamics and warmth transfer performance. Well-designed nozzles lessen turbulence, limit pressure drops, and assist a consistent glide sample. Materials along with chrome steel or high-grade alloys are normally used to face up to the pressures and temperatures concerned. Nozzles can be welded or flanged, relying at the software. Regular inspection guarantees they stay free of blockages, corrosion, or misalignment. Even minor nozzle damage can cause leaks or inefficient warmness alternate. Proper sizing and placement are essential for reaching uniform go with the flow, which in turn helps efficient thermal transfer and operational safety in industrial procedures.
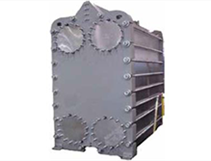
Heat Transfer Surfaces and Their Efficiency
Heat switch surfaces are many of the most essential warmth exchanger components, directly influencing the tool’s efficiency. These surfaces facilitate the actual thermal power trade between fluid streams. In spiral heat exchangers, the spiral channels shaped by way of metal plates act as prolonged surfaces that maximize contact vicinity even as promoting turbulence, improving warmth transfer rates. Clean, easy surfaces beautify power transfer and decrease fouling. Contaminants, scaling, or corrosion can substantially lessen floor effectiveness, inflicting power loss and capability machine failure. Surface treatment techniques like coating or sprucing can improve resistance to scaling and corrosion. The geometry of the floor—flat, corrugated, or spiraled—additionally performs a position in how efficiently warmness is transferred. Investing in long lasting and high-overall performance substances for these surfaces ensures most excellent operation and energy efficiency across diverse applications.
Baffles and Their Contribution to Flow Control
Baffles are inner additives used to direct fluid float inside warmness exchanger structures. These warmth exchanger components help improve warmth transfer by means of growing turbulence and making sure fluid flows throughout the warmth switch surfaces rather than taking an immediate direction. In spiral heat exchangers, the spiral design itself frequently gets rid of the want for traditional baffles, because the channel configuration clearly promotes controlled glide. However, in many other designs, baffles stay crucial for enhancing warmth change efficiency. Poorly placed or damaged baffles can create useless zones, reduce overall performance, and make a contribution to uneven heating or cooling. Constructed from long lasting metals, baffles should face up to mechanical stress and fluid-brought about vibration. Regular inspection and maintenance are important to save you cracking or loosening. Properly designed and maintained baffles make a contribution to most reliable go with the flow distribution, improved turbulence, and in the long run, better warmth transfer performance.
The Role of End Covers in System Integrity
End covers seal the extremities of warmth exchangers, enclosing internal components and maintaining machine strain. These warmth exchanger elements must face up to thermal enlargement, strain versions, and environmental exposure. In spiral warmness exchangers, quit covers also permit access for cleaning and preservation, making them important for operational durability. The fabric of end covers ought to suit or complement the warmth exchanger shell to keep away from galvanic corrosion. They are generally fixed with bolts or clamps, and gaskets are used to create a decent seal. If end covers end up warped or corroded, the whole heat exchanger may lose performance or leak risky fluids. Well-maintained quit covers make certain safety, ease of carrier, and solid operation. Their role in securing internal additives and preserving typical structural integrity can not be underestimated in any industrial warmth switch gadget.
Importance of Tie Rods and Spacers in Heat Exchangers
Tie rods and spacers are structural warmness exchanger parts that assist preserve the alignment and spacing of plates or internal components. These factors are vital in ensuring that plates do no longer shift underneath strain or vibration, which is specially important in spiral heat exchangers in which continuous waft paths are critical. Tie rods also undergo the mechanical load when the warmth exchanger is below pressure. Made from excessive-strength substances, they need to withstand corrosion and mechanical fatigue. Spacers assist keep constant gaps between warmth transfer surfaces, that is critical for retaining uniform flow and optimal thermal performance. Without proper guide, the inner structure may additionally deform, main to inefficient heat transfer or mechanical failure. Monitoring the situation of tie rods and spacers guarantees the stableness and efficiency of the entire warmness exchanger meeting.
Drain and Vent Connections for Maintenance and Safety
Drain and vent connections are vital heat exchanger elements used all through renovation, cleansing, and stress remedy operations. These ports permit for the elimination of residual fluids and gases that would have an effect on performance or protection. In spiral heat exchangers, the compact design can also combine drain and vent functions into the shell or cowl plates for smooth get admission to. Regular use of drain ports prevents infection and guarantees proper shutdown tactics. Vent connections assist release trapped air or gas, preserving device stress and flow consistency. Both components ought to be built of corrosion-resistant materials and outfitted with suitable valves. Their placement and accessibility have an effect on how without problems a warmness exchanger may be cleaned or serviced. Efficient use of those components helps secure, hygienic, and dependable operation across all kinds of fluid processing industries.
Thermal Expansion Joints and System Flexibility
Thermal enlargement joints permit heat exchangers to flex in response to temperature fluctuations, preventing stress fractures or leaks. These specialised warmness exchanger components are designed to absorb mechanical movement and thermal strain between fixed elements. Spiral warmness exchangers, recognised for his or her compact design, may contain flexible joints in piping connections or in the shell structure to deal with adjustments throughout operation. Without these joints, thermal biking may want to cause cracked additives or misaligned fittings. Proper selection of growth joints based totally on temperature variety, pressure, and chemical compatibility ensures durability and protection. Regular inspection facilitates discover wear, corrosion, or fatigue that might cause leaks. Including thermal growth joints in machine design considerably complements the sturdiness and overall performance of the warmth exchanger whilst safeguarding in opposition to thermal stress.
Maintenance Tools and Accessories for Heat Exchanger Parts
Maintenance gear and accessories are indispensable to making sure the overall performance of numerous warmth exchanger components. From cleaning brushes to hydraulic plate pullers and diagnostic kits, these equipment simplify inspection and servicing responsibilities. Spiral warmth exchangers, in particular, may require specialised device for cleansing the spiral channels and checking gasket integrity. Preventative renovation add-ons consisting of protective covers, pressure gauges, and drift meters aid the continued overall performance and reliability of the gadget. Using proper equipment guarantees that inner parts aren’t damaged all through cleaning or inspection. Scheduled use of those gear allows pick out minor troubles earlier than they increase into pricey maintenance. A nicely-equipped upkeep recurring not best extends the existence of heat exchanger additives however additionally contributes to electricity efficiency and machine uptime across diverse business programs.
Enhancing Efficiency with Quality Heat Exchanger Parts
Investing in first rate heat exchanger elements is the muse of an efficient and long-lasting thermal system. Whether the use of traditional designs or spiral heat exchangers, each aspect—from plates and gaskets to nozzles and baffles—need to be selected with care. The preference of materials, precision in design, and regular renovation practices all contribute to a device’s overall performance. Spiral warmth exchangers, especially, gain from streamlined waft paths and fewer fouling issues, supplied that all parts are nicely installed and maintained. Understanding the function of each component enables in making knowledgeable choices for the duration of procurement, set up, and upkeep. When warmth exchanger elements are stored in best condition, they support higher power use, lower renovation charges, and increased operational reliability. Prioritizing first-rate components and expert servicing ensures that your heat exchanger device performs at its pleasant for future years.